Omega Speedmaster Clutch Action in Slow Motion
Gav Free, of The Slo Mo Guys, takes an up close look at his Omega Speedmaster Dark Side of the Moon in slow motion.
10,000 frames per second is where things start to get interesting and I wish Gavin had been able to dial things in even slower.
The ricochet action between the gears of the sliding clutch mechanism hint at similarly violent, sub-millisecond interactions happening between the pallet fork and the escape wheel. The audio waveform of the interaction at the escapement, which can readily be captured at at an even higher sample rate, also hints at the notable forces that are at play here. There is an old, internal, slow-motion video showcasing the interaction of the escapement that circulates around Rolex every now and then. To recount the words of one watchmaker, "It looks like a train wreck."
The fact that we have so adeptly learned to harness and control this energy with such a high degree of repeatability and precision remains remarkable.
Gav's comment shortly after the eleven minute mark, about only leaving the brightest of the lights he employed on for a few seconds at a time so as not to cook the watch, was warranted and even a bit tardy. It was clear from the close-up shots of the escapement earlier in the footage that nearly all of the lubricant at the pallets had already evaporated, most likely from heat given off by the large, primary spotlight. Speaking from experience, having filmed a number of close-up shots under powerful lights back in the day for Alliance Horlogère, it doesn't take long for watch lubricants to evaporate under that kind of exposure.
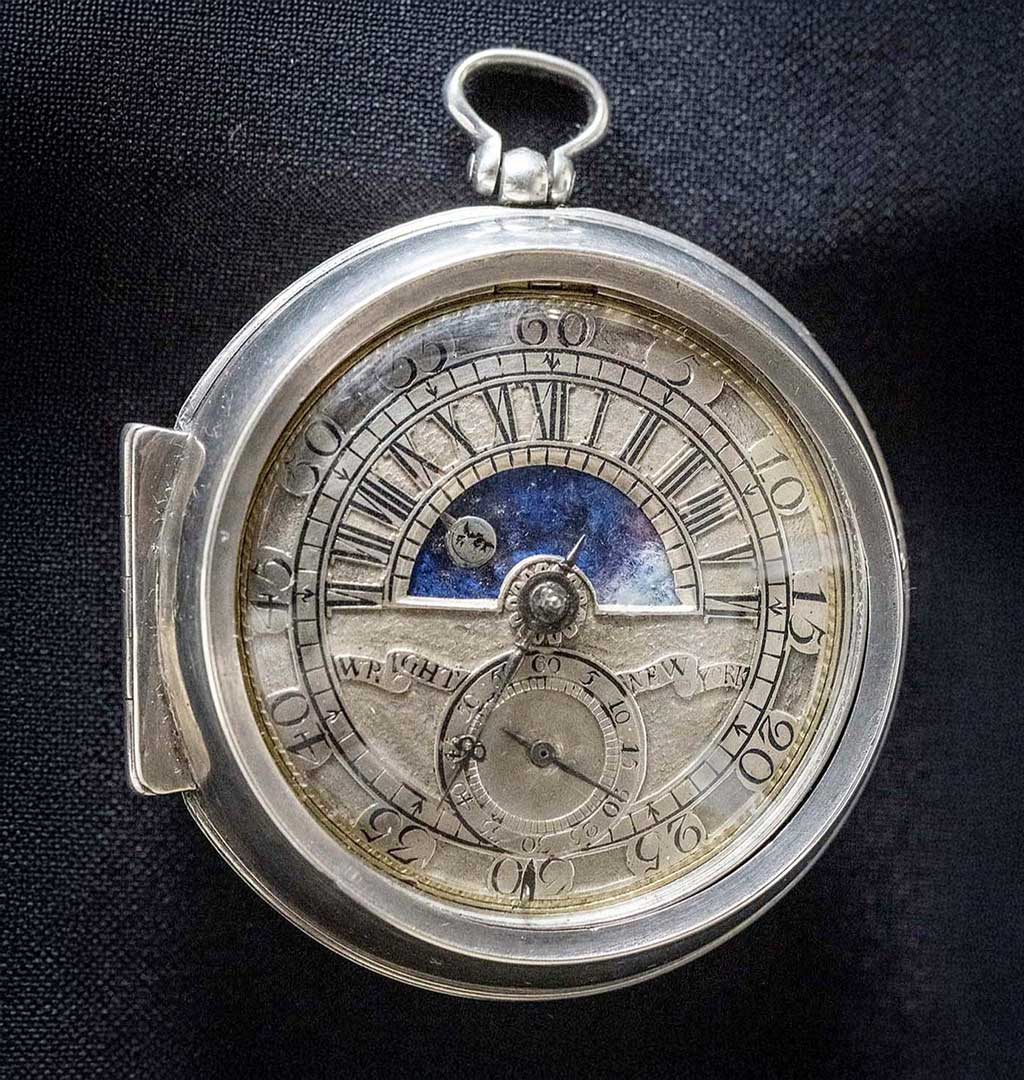
Earliest Known American Watch
Crafted around 1715 this pocket watch is the earliest known pocket watch composed on American soil. The timepiece was created by John Wright, an English watchmaker from Liverpool who immigrated to New York circa 1711.
The sun and moon indication is an admirable touch.
Andreas Strehler on the Artistry of Watchmaking
Independent watchmaker, Andreas Strehler, in an interview with Pascal Brandt at Monochrome:
I’m not very influenced by the watch market. I feel more like an artist who creates to surprise the public.
Mechanical watches are like music. Gears have been known for centuries, like the musical notes that have been defined since Bach. We can create a new mechanism every day, like new songs that can be composed and sung.
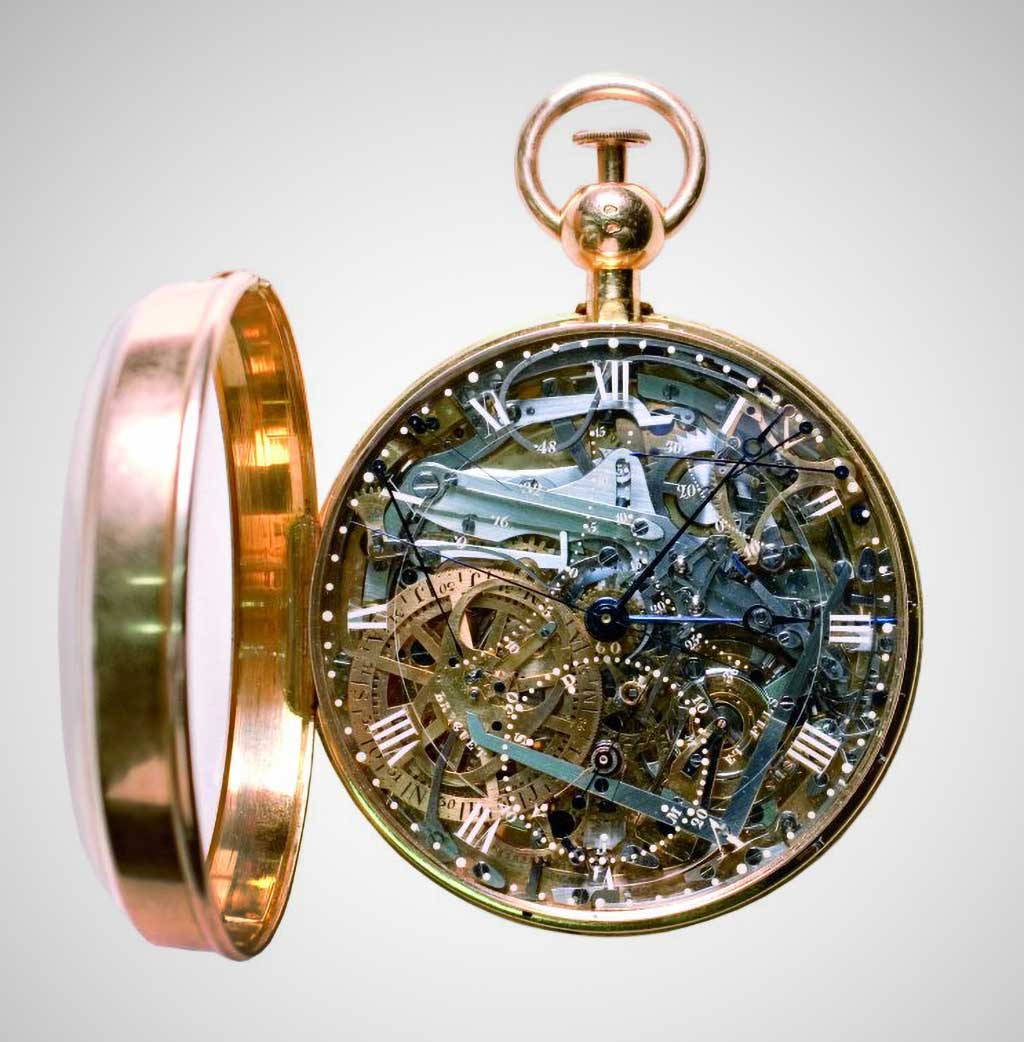
Breguet's Marie Antoinette in London
Infamous and complex, Breguet pocket watch No. 160, The Marie Antoinette, is part of the Versailles: Science and Splendour Exhibit on display at the London Science Museum from December 12th, 2024 through April 21st, 2025.
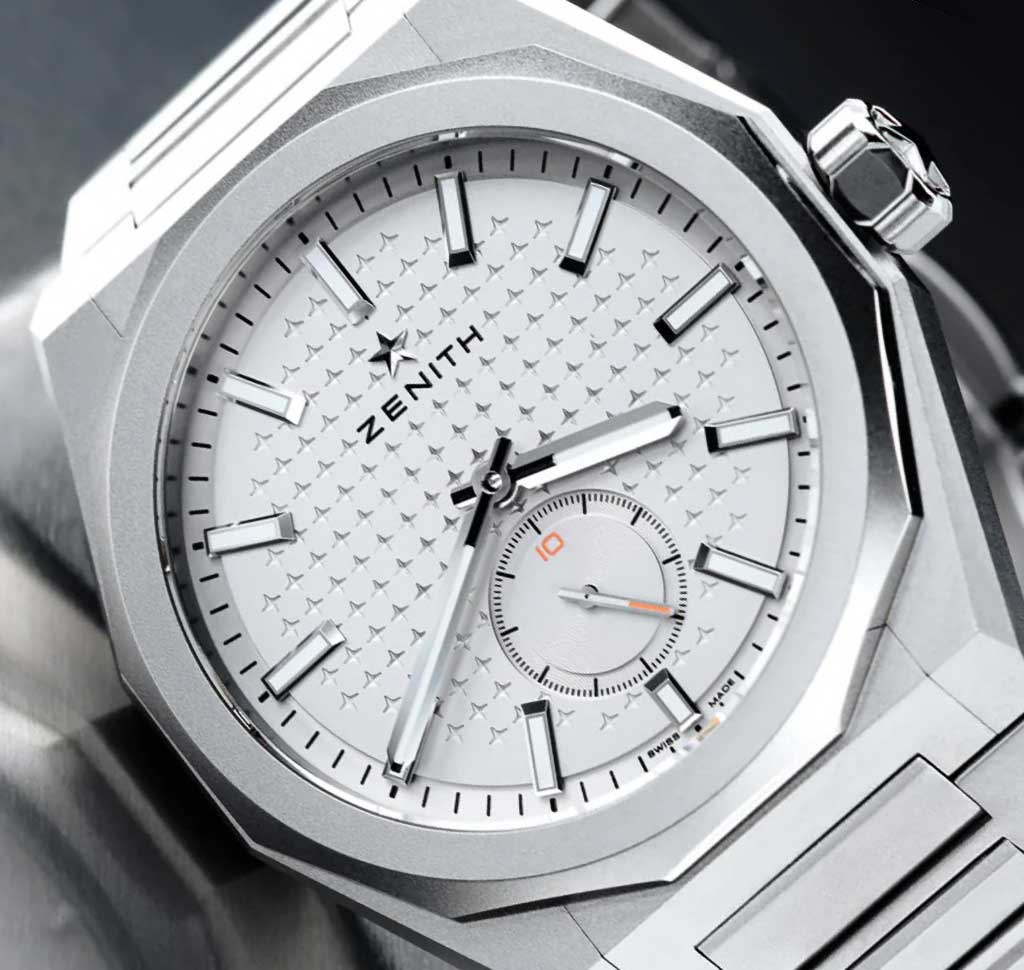
Zenith DEFY Skyline C.X
A pleasant use of depth in the dial of this collaboration between Zenith and Collective Horology, inspired by mid-century modern industrial design. The touch of colour is reminiscent of the orange accents leveraged by the design teams at Nomos and Apple.
The State of Legacy Watchmakers
Ariel Adams, writing for A Blog to Watch, on the contrast between incumbent and independent watchmakers in 2024:
A company with a 100, 150, or 250-year history lingering in the air will have a different approach to decisions and communication than a first-generation one that is balancing right on the edge of its cash flow reserves. And yet, it feels like historical companies struggle with turning their established present and solid foundations into calmness, confidence, and a sight on the distant future — instead, sometimes all we get is stuffiness, condescension, and an obsession with the past.
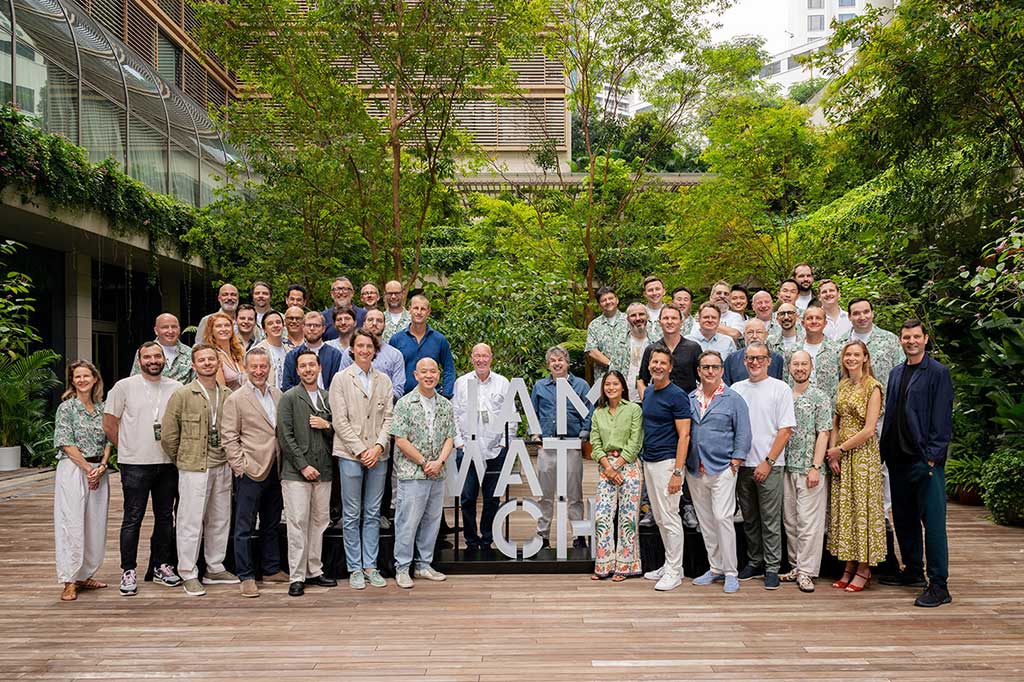
An Astounding Array of Independents
Michael Tay, of The Hour Glass, drew an astonishing array of the world's top horological talent together in Singapore for Iamwatch 2024.
Some thoughtful perspective on the event from JX Su, reporting for Watches by SJX.
The watchmaking-themed Hawaiian shirts were a fun touch for an event held in such a tropical locale.
Additional reporting, and loads more photos of the event, from Mark Kauzlarich over at Hodinkee.
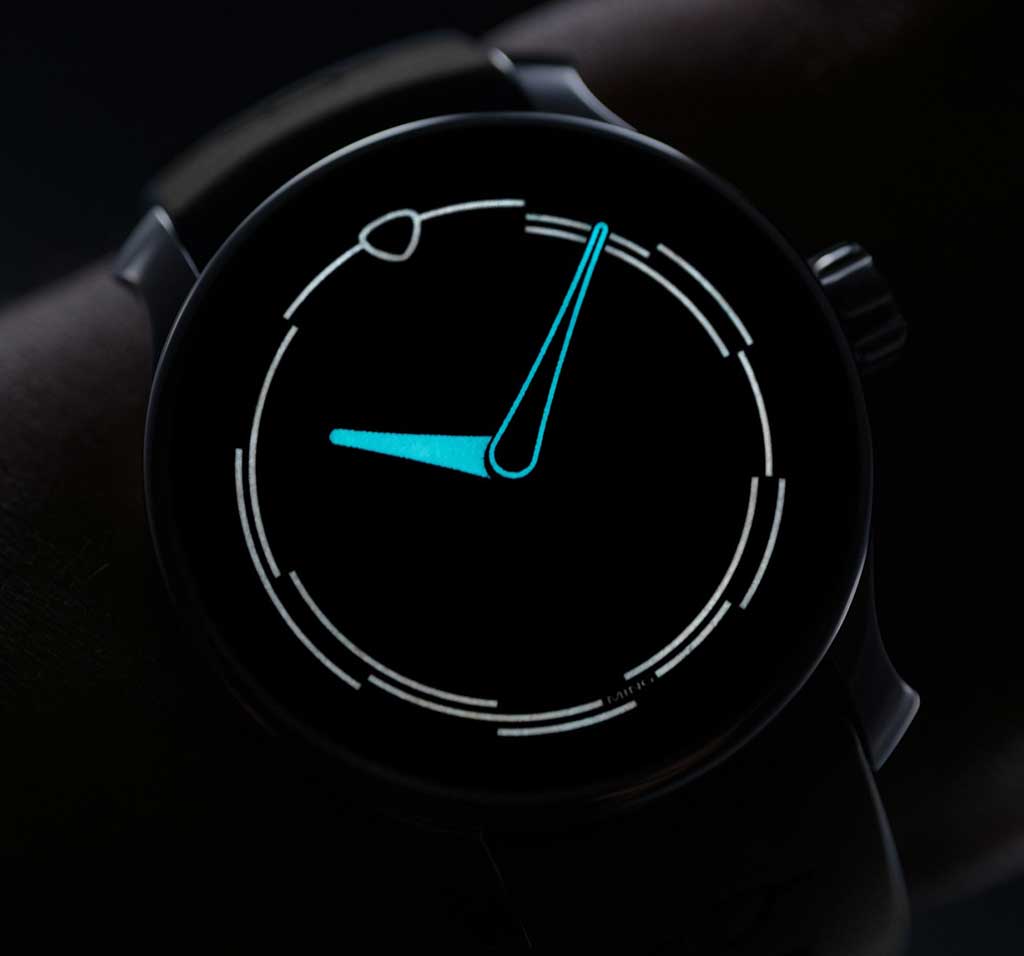
White Lume
The Ming Minimalist, reference 37.02, heralds in the era of a mass-produced watch being available with luminous pigment that not only looks white in daylight, but glows white in the dark.
The 37.02 Minimalist is also the first timepiece from Ming that has been designed, engineered and production managed at their new Swiss facility in La Chaux de Fonds.
Kelo Wood
Following the path of an unsetting sun across the sky in the summer months, pine trees north of the Arctic Circle develop a coil-like grain structure that imbues the trunks of the trees with an abnormal level of strength and durability relative to their straight-grained counterparts. So much so, that kelo trees remain standing long after they have died, shedding their bark while still erect, allowing the sapwood to dry and become bleached by the sun. The resulting timber is likewise strong, as well as being unusually resistant to rot and warpage. Kelo wood also boasts a characteristic colouration: greyish-white on the outside with reddish-brown heartwood.
Kello, which is the Finnish word for clock, shares the same Finno-Ugric root as kelo. While the etymology of the words themselves are believed to have been derived from the word for bell—just as clock is in English—the inherent qualities of both clock dials and kelo wood are protracted from the relative motion of the sun across the sky in the Northern Hemisphere.